Verschweißen von PE-Schaumstoffen
Für Schutz-, Fixier- und Isolierelemente, Einlagen und Einsätze sowie Sandwichpaneele verschweißen wir mikroporöse Polyethylenplatten mit geschlossener Zellstruktur: NOPASMART, NOPAPLANK, ARPLANK, XPE, iPLANK.
Wir verschweißen auch zwei verschiedene Arten von PE-Schaumstoffen.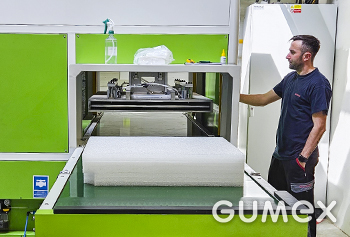
Maschinenparameter:
- Arbeitsfläche 800 x 1 200 x 400 mm (B x L x H).
- Maximale Anzahl der zu verschweißenden Schichten: 11 (Gesamthöhe max. 400 mm).
Tipp:
- Wenn die Einsätze oder Einlagen kleiner sind, können wir mehrere Stück auf einmal verschweißen – sie werden dann auf einer Fläche von bis zu 800 x 1200 mm angeordnet.
- Größere Einsätze oder Einlagen werden nach der derzeit bewährten Methode hergestellt: einer Kombination aus Schaumstoffen und Selbstklebematerialien.
Senden Sie uns Ihre Anfrage
Vorteile dieser Technologie
- Saubere und umweltfreundliche Verbindung ohne Klebstoffe
- Starke und dauerhafte Verbindungen
- Mehrlagige Verbindungsmöglichkeit
- Niedrige Betriebskosten im Vergleich zum Klebe- oder Fräsverfahren (der Preis ist immer individuell und hängt von der Komplexität der Einlage oder des Einsatzes ab)
- Schnelles Verfahren
- Möglichkeit der Automatisierung und Wiederholbarkeit der Produktion (Speicherung von Programmen für verschiedene Auftragstypen)
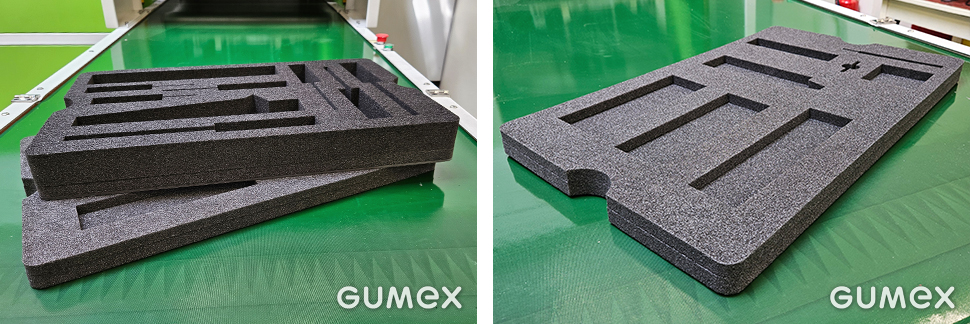
Einschränkung:
- Beim Verschweißen von Schaumstoffen ist je nach Art und Dichte des Schaumstoffs ein Materialverlust von 0,5 - 3 mm pro Lage zu rechnen. Dies ist darauf zurückzuführen, dass der Schaumstoff beim Erhitzen aufgeschmolzen wird (dadurch entsteht eine „klebrige“ Schicht). Beispiel: Es werden 4 Schichten von je 20 mm vorbereitet (vor dem Schweißen beträgt die Gesamthöhe 80 mm). Die Maschine nimmt die oberste Schicht, erhitzt sie und dabei gehen etwa 2 mm an Dicke verloren. Nach der Beendigung des Schweißverfahrens beträgt die Dicke der einzelnen Schichten 18; 18; 18; 20 mm = 74 mm. (die letzte Schicht wird nicht erhitzt). Unserer Erfahrung nach haben wir jedoch in der Regel bereits Ausgangsmaterialien mit einer gewissen Plus-Dickentoleranz, so dass der Verlust pro Schicht nicht so bedeutend ist. Für die Serienproduktion liefern wir in der Regel ein Muster, das vom Kunden freigegeben wird, damit er genau sieht, wie dick das Endprodukt tatsächlich ist.
- Limitierend ist immer die Dicke der ersten Schicht (z. B. der Boden der Einlage oder des Einsatzes). Diese Bodendicke, also die Basisschicht, sollte – da dieses durch das Greifersystem der Maschine bedingt ist – idealerweise 15 mm betragen. Aber auch diese Einschränkung lässt sich zum Vorteil der Sache umkehren: die ersten beiden Schichten werden „umgekehrt“ verschweißt, dann umgedreht und dann können wir mit den nächsten Schichten fortfahren. Es ist halt zeitaufwändiger, aber machbar.
- Einige strukturierte oder zu weiche Schaumstoffe sind schwer zu verschweißen: Das Material EVA (aus EVA-PE-Material) wird mit dieser Technologie nicht verschweißt (EVA-Schaumstoff lässt sich nicht gut aufschmelzen), bzw. dieses Material wird als die Sichtschicht eingesetzt, d.h. Auf das EVA-Material werden die PE-Schaumstoffe aufgeschweißt.
- Bei den Kunden sind auch Einlagen und Einsätze aus mikroporösen Gummis, z.B. T130 EP, beliebt. Mit der Schweißmaschine verschweißen wir diese Art von Material nicht. Einlagen und Einsätze aus diesen Materialien werden in Kombination mit einem Selbstklebematerial hergestellt.
- Genaue Temperatur- und Druckeinstellungen sind unerlässlich - sonst kann sich der Schaumstoff verformen
Schweißprinzip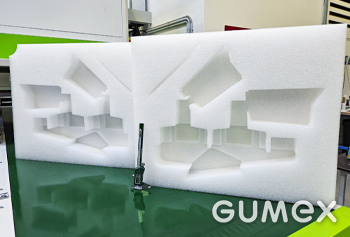
- Vorbereitung, Ausrichtung der PE-Schaumstoffschichten.
- Das Heizelement (in diesem Fall eine Teflonplatte) wird auf die gewünschte Temperatur erhitzt. (PE-Schaumstoffe werden in der Regel bei 100-140 °C oberflächlich aufgeschmolzen.).
- Der Schaumstoff wird mit der erhitzen Platte angedrückt.
- Abkühlen und Fixieren – die Verbindung wird abgekühlt, um zu erstarren und eine feste Verbindung zu bilden.
Welche Produkte wir für Sie mit der Technologie des PE-Schaumstoffschweißens herstellen können:
- Einlagen und Einsätze (Transporteinsätze, Schutzeinlagen)
-
Organizer
TIPP: Fordern Sie unsere Musterkarte mit Materialien für Schaumstoffeinlagen/-einsätze!
Schaumstoffeinlagen und -einsätze sowie Organizer schützen zuverlässig Ihre Produkte, Geräte, Werkzeuge und Produktmuster!
Für Schutz-, Fixier- und Isolierelemente, Einlagen und Einsätze sowie Sandwichpaneele verschweißen wir mikroporöse Polyethylenplatten mit geschlossener Zellstruktur: NOPASMART, NOPAPLANK, ARPLANK, XPE, iPLANK.
Wir verschweißen auch zwei verschiedene PE-Schaumtypen miteinander (mit Ausnahme von XPE-Platten, die nur miteinander verschweißt werden können, d. h. XPE/XPE, nicht mit Platten aus einem anderen PE-Schaumtyp).
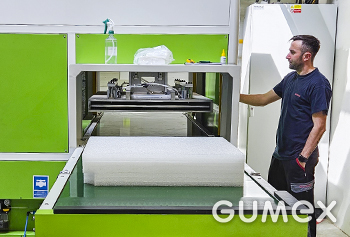
Maschinenparameter:
- Arbeitsfläche 800 x 1 200 x 400 mm (B x L x H).
- Maximale Anzahl der zu verschweißenden Schichten: 11 (Gesamthöhe max. 400 mm).
Tipp:
- Wenn die Einsätze oder Einlagen kleiner sind, können wir mehrere Stück auf einmal verschweißen – sie werden dann auf einer Fläche von bis zu 800 x 1200 mm angeordnet.
- Größere Einsätze oder Einlagen werden nach der derzeit bewährten Methode hergestellt: einer Kombination aus Schaumstoffen und Selbstklebematerialien.
Senden Sie uns Ihre Anfrage
Vorteile dieser Technologie
- Saubere und umweltfreundliche Verbindung ohne Klebstoffe
- Starke und dauerhafte Verbindungen
- Mehrlagige Verbindungsmöglichkeit
- Niedrige Betriebskosten im Vergleich zum Klebe- oder Fräsverfahren (der Preis ist immer individuell und hängt von der Komplexität der Einlage oder des Einsatzes ab)
- Schnelles Verfahren
- Möglichkeit der Automatisierung und Wiederholbarkeit der Produktion (Speicherung von Programmen für verschiedene Auftragstypen)
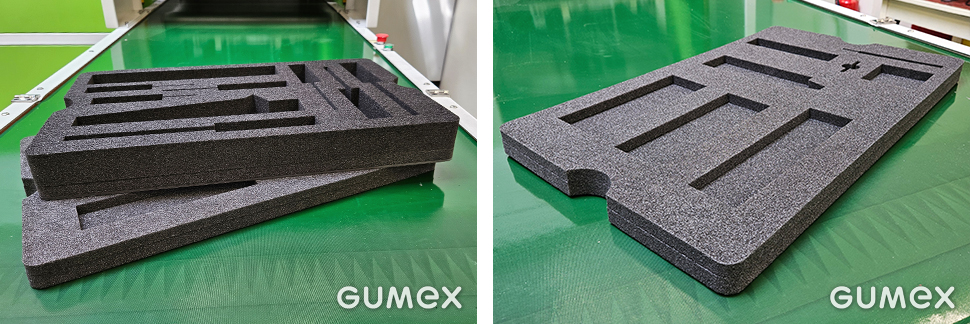
Einschränkung:
- Beim Verschweißen von Schaumstoffen ist je nach Art und Dichte des Schaumstoffs ein Materialverlust von 0,5 - 3 mm pro Lage zu rechnen. Dies ist darauf zurückzuführen, dass der Schaumstoff beim Erhitzen aufgeschmolzen wird (dadurch entsteht eine „klebrige“ Schicht). Beispiel: Es werden 4 Schichten von je 20 mm vorbereitet (vor dem Schweißen beträgt die Gesamthöhe 80 mm). Die Maschine nimmt die oberste Schicht, erhitzt sie und dabei gehen etwa 2 mm an Dicke verloren. Nach der Beendigung des Schweißverfahrens beträgt die Dicke der einzelnen Schichten 18; 18; 18; 20 mm = 74 mm. (die letzte Schicht wird nicht erhitzt). Unserer Erfahrung nach haben wir jedoch in der Regel bereits Ausgangsmaterialien mit einer gewissen Plus-Dickentoleranz, so dass der Verlust pro Schicht nicht so bedeutend ist. Für die Serienproduktion liefern wir in der Regel ein Muster, das vom Kunden freigegeben wird, damit er genau sieht, wie dick das Endprodukt tatsächlich ist.
- Limitierend ist immer die Dicke der ersten Schicht (z. B. der Boden der Einlage oder des Einsatzes). Diese Bodendicke, also die Basisschicht, sollte – da dieses durch das Greifersystem der Maschine bedingt ist – idealerweise 15 mm betragen. Aber auch diese Einschränkung lässt sich zum Vorteil der Sache umkehren: die ersten beiden Schichten werden „umgekehrt“ verschweißt, dann umgedreht und dann können wir mit den nächsten Schichten fortfahren. Es ist halt zeitaufwändiger, aber machbar.
- Einige strukturierte oder zu weiche Schaumstoffe sind schwer zu verschweißen: Das Material EVA (aus EVA-PE-Material) wird mit dieser Technologie nicht verschweißt (EVA-Schaumstoff lässt sich nicht gut aufschmelzen), bzw. dieses Material wird als die Sichtschicht eingesetzt, d.h. Auf das EVA-Material werden die PE-Schaumstoffe aufgeschweißt.
- Bei den Kunden sind auch Einlagen und Einsätze aus mikroporösen Gummis, z.B. T130 EP, beliebt. Mit der Schweißmaschine verschweißen wir diese Art von Material nicht. Einlagen und Einsätze aus diesen Materialien werden in Kombination mit einem Selbstklebematerial hergestellt.
- Genaue Temperatur- und Druckeinstellungen sind unerlässlich - sonst kann sich der Schaumstoff verformen
Schweißprinzip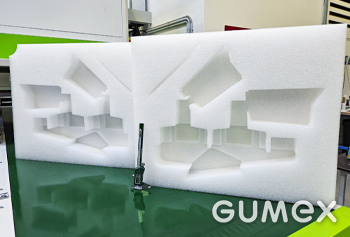
- Vorbereitung, Ausrichtung der PE-Schaumstoffschichten.
- Das Heizelement (in diesem Fall eine Teflonplatte) wird auf die gewünschte Temperatur erhitzt. (PE-Schaumstoffe werden in der Regel bei 160-0 °C oberflächlich aufgeschmolzen.).
- Der Schaumstoff wird mit der erhitzen Platte angedrückt.
- Abkühlen und Fixieren – die Verbindung wird abgekühlt, um zu erstarren und eine feste Verbindung zu bilden.
Welche Produkte wir für Sie mit der Technologie des PE-Schaumstoffschweißens herstellen können:
- Einlagen und Einsätze (Transporteinsätze, Schutzeinlagen)
-
Organizer
TIPP: Fordern Sie unsere Musterkarte mit Materialien für Schaumstoffeinlagen/-einsätze!
Schaumstoffeinlagen und -einsätze sowie Organizer schützen zuverlässig Ihre Produkte, Geräte, Werkzeuge und Produktmuster!